As First Author
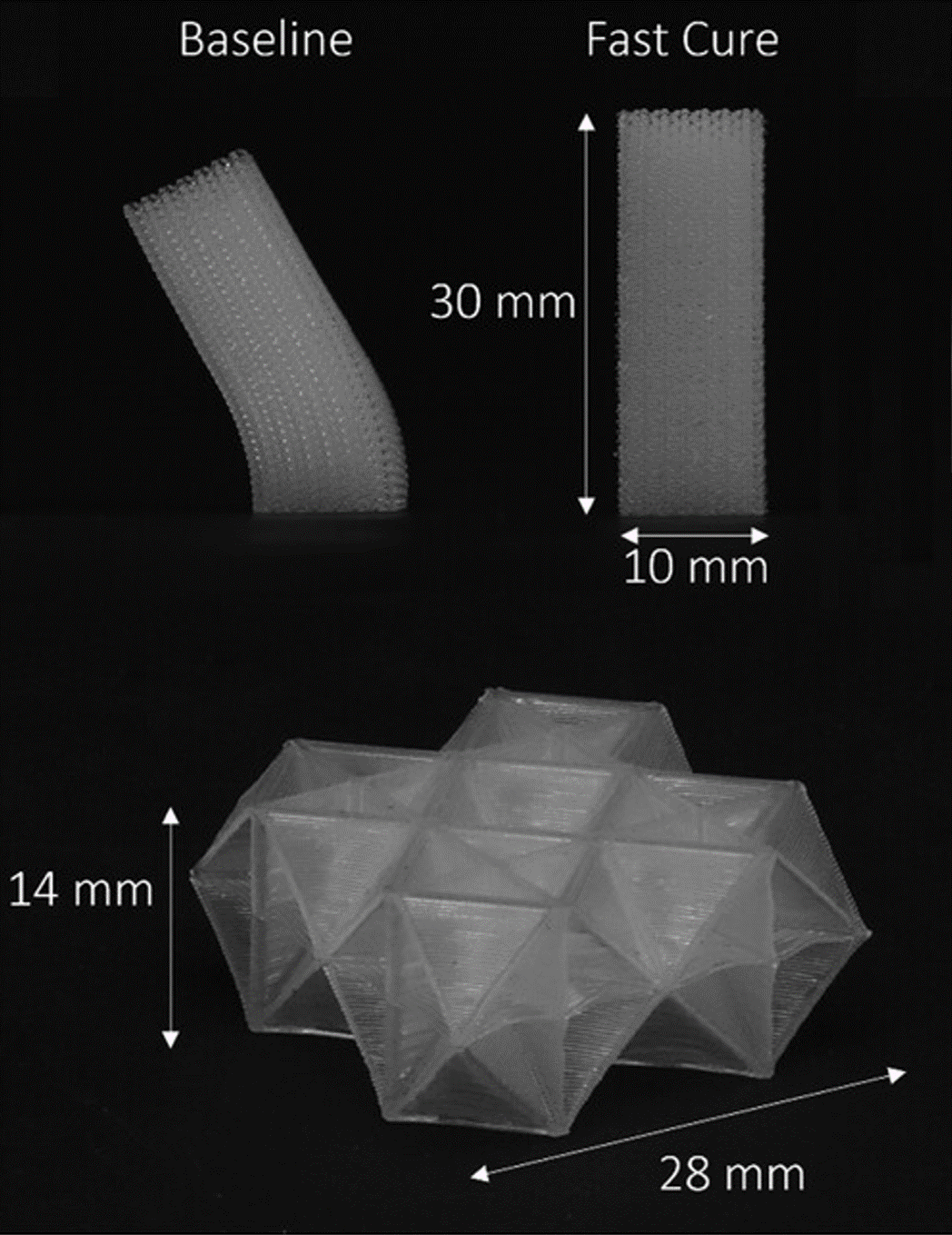
A. Guell Izard, L. X. Pérez Pérez, T. H. Weisgraber, I. M. Van Meerbeek, A. M. Golobic, E. B. Duoss, J. M. Lenhardt (2024), Novel Fast Cure Silicone Inks for Single-Step, Support-Free 3D Printing of Tall, Overhanging, and High Aspect Ratio Structures, Advanced Materials Technologies
Silicone elastomers have a broad variety of applications, such as soft robotics, biomedical devices, and structural metamaterials. The extrusion-based method known as direct ink write (DIW) has enabled the production of additively manufactured silicone structures. However, this method is limited to manufacturing mostly planar or pseudo-3D structures. Due to the low self-supporting capabilities of extruded strands for traditional silicone-based “inks,” obtaining tall or overhanging structures, or structures comprised by thin walls is not feasible. Here, a novel Fast Cure silicone-based ink is demonstrated that enables manufacturing of complex 3D structures. The Fast Cure ink is a two-part mixture and silicone structures are produced by inline mixing and coextrusion of a part containing a catalyst (part A) and a part containing a crosslinker (part B). By the virtue of crosslinking, the extruded strands rapidly rigidize, increasing their self-supportive capacity. Hence, structures can be obtained with superior shape retention and previously unobtainable parts are realized that are tall, with aspect ratios higher than 3, and have overhanging features, achieving inclination angles smaller than 35° with respect to the printing plane. These minimal sag parts are achieved without requiring extra curing or mechanisms, support structures, or suspension baths.
(The image displayed has been extracted from Figure 5 of the main manuscript)

A. Guell Izard, E. P. Garcia, M. Dixon, E. O. Potma, T. Baldacchini, L. Valdevit (2020), Enhanced Adhesion in Two-Photon Polymerization Direct Laser Writing, AIP Advances
We have quantified the adhesion forces between two-photon polymerization direct laser writing (TPP-DLW) microstructures and glass surfaces with and without an adhesion promoter. Glass surfaces treated with an acryloxy-silane agent produce adhesion forces that are almost three times larger than the forces observed with pristine glass surfaces. Determination of the substrates’ surface free energies suggests that the observed adhesion enhancement is chemical in its nature, implying that covalent bonds are formed between the polymer and the glass by means of the silane agent. The importance of this finding is demonstrated in the successful production of glassy carbon microstructures using TPP-DLW, followed by pyrolysis.

A. Guell Izard, L. Valdevit (2020), Magnetoelastic Metamaterials for Energy Dissipation and Wave Filtering, Advanced Engineering Materials
A novel magnetoelastic mechanical metamaterial consisting of a hyperelastic 2D lattice incorporating permanent magnets is presented and characterized. When properly designed and fabricated, the metamaterial possesses two stable equilibrium configurations (henceforth referred to as hexagonal/hourglass and kagome), both stretching dominated (and hence stiff). The two configurations have significantly different elastic properties and wave propagation characteristics, as shown numerically and experimentally. By switching between the two configurations via uniaxial loading cycles, the material displays hysteresis, thus dissipating substantial amounts of energy; in contrast with purely mechanical bistable structures (e.g., arches, hinged beams and buckled beams), the proposed magnetoelastic metamaterial does not require multiple unit cells in series or stiff boundary conditions to exhibit energy dissipation, thus enabling the implementation of compact stiff dampers. The presence of a bandgap in the kagome configuration (but not in the hexagonal/hourglass configuration) is attributed to an internal resonance mechanism and provides the foundation for the development of compact dynamic filters for mechanical signals.
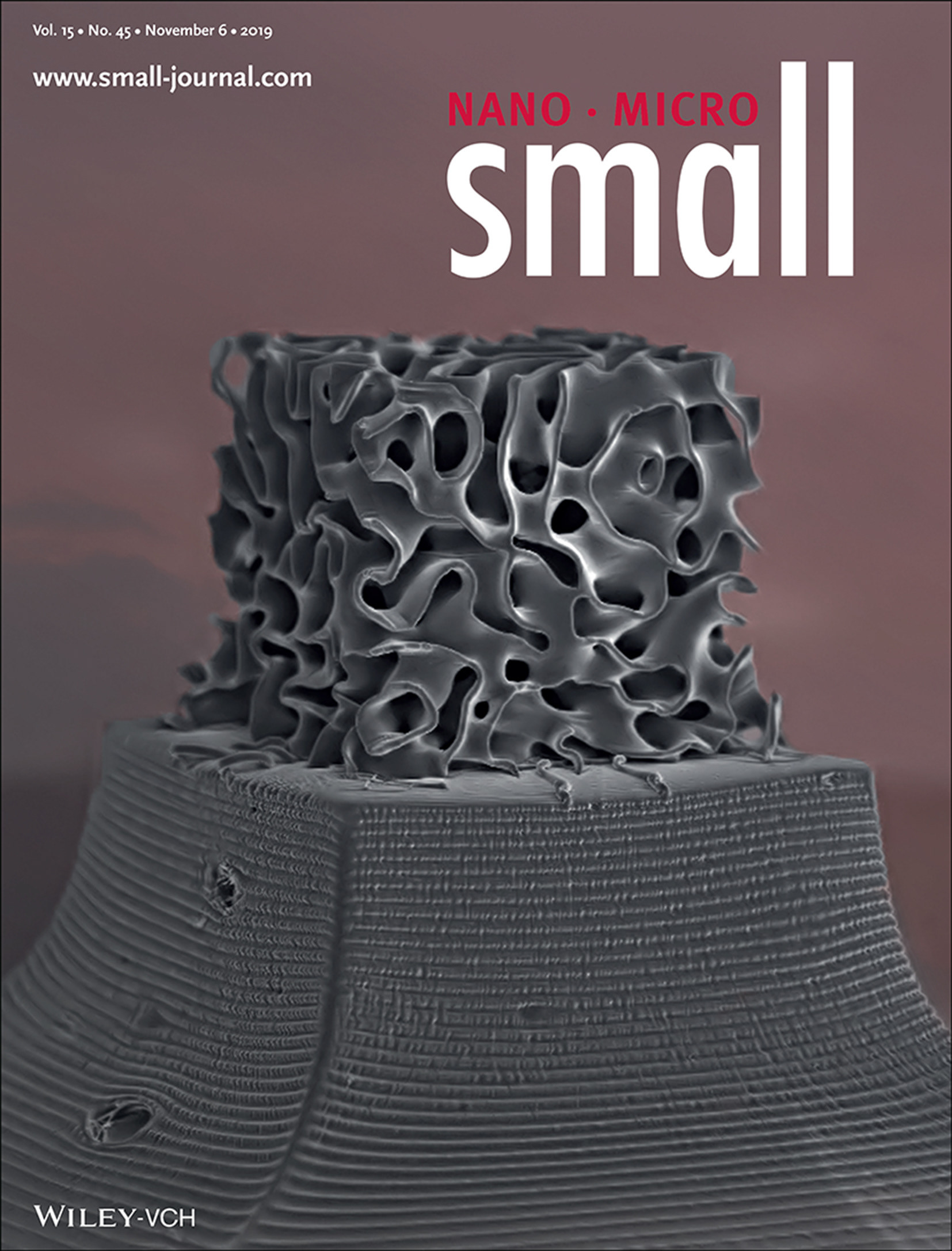
A. Guell Izard, J. Bauer, C. Crook, V. Turlo, L. Valdevit (2019), Ultrahigh Energy Absorption Multifunctional Spinodal Nanoarchitectures, Small
Nanolattices are promoted as next‐generation multifunctional high‐performance materials, but their mechanical response is limited to extreme strength yet brittleness, or extreme deformability but low strength and stiffness. Ideal impact protection systems require high‐stress plateaus over long deformation ranges to maximize energy absorption. Here, glassy carbon nanospinodals, i.e., nanoarchitectures with spinodal shell topology, combining ultrahigh energy absorption and exceptional strength and stiffness at low weight are presented. Noncatastrophic deformation up to 80% strain, and energy absorption up to one order of magnitude higher than for other nano‐, micro‐, macro‐architectures and solids, and state‐of‐the‐art impact protection structures are shown. At the same time, the strength and stiffness are on par with the most advanced yet brittle nanolattices, demonstrating true multifunctionality. Finite element simulations show that optimized shell thickness‐to‐curvature‐radius ratios suppress catastrophic failure by impeding propagation of dangerously oriented cracks. In contrast to most micro‐ and nano‐architected materials, spinodal architectures may be easily manufacturable on an industrial scale, and may become the next generation of superior cellular materials for structural applications.
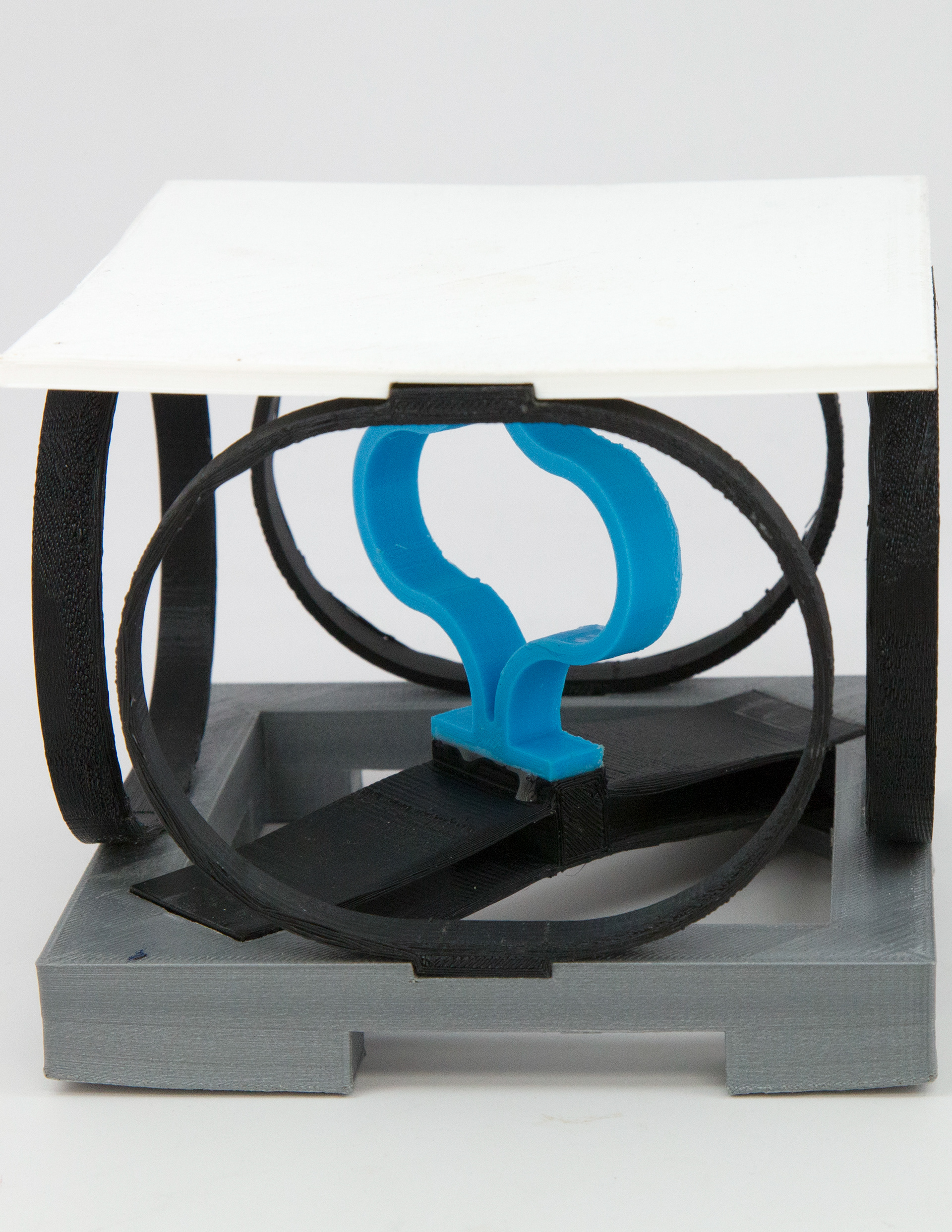
A. Guell Izard, R. Fabian Alfonso, G. McKnight, L. Valdevit (2017), Optimal Design of a Cellular Material Encompassing Negative Stiffness Elements for Unique Combinations of Stiffness and Elastic Hysteresis, Materials & Design
Viscoelastic materials are commonly used to dissipate kinetic energy in case of impact and vibrations. Unfortunately, dissipating large amounts of energy in a monolithic material requires high combinations of two intrinsic properties – Young's modulus and loss factor, which are generally in conflict. This limitation can be overcome by designing cellular materials incorporating negative stiffness elements. Here we investigate a configuration comprising two positive stiffness elements and one negative stiffness element. This unit cell possesses an internal degree of freedom, which introduces hysteresis under a loading-unloading cycle, resulting in substantial energy dissipation, while maintaining stiffness. We demonstrate and optimize a simple implementation in a single material design that does not require external stabilization or pre-compression of buckled elements; these key features make it amenable to fabrication by virtually any additive manufacturing approach (from 3D printing to assembly and brazing) in a wide range of base materials (from polymers to metals). No additional intrinsic damping mechanism is required for the base material, which is assumed linear elastic. Furthermore, the architected material can be designed to be fully recoverable. When optimized, these architected materials exhibit extremely high combinations of Young's modulus and damping, far superior to those of each constituent phase.
More Publications
W. Zhou, S. Nadarajah, L. Li, A. Guell Izard, H. Yan, A. K. Prachet, P. Patel, X. Xia, C. Daraio (2025), 3D polycatenated architected materials, Science
Architected materials derive their properties from the geometric arrangement of their internal structural elements. Their designs rely on continuous networks of members to control the global mechanical behavior of the bulk. In this study, we introduce a class of materials that consist of discrete concatenated rings or cage particles interlocked in three-dimensional networks, forming polycatenated architected materials (PAMs). We propose a general design framework that translates arbitrary crystalline networks into particle concatenations and geometries. In response to small external loads, PAMs behave like non-Newtonian fluids, showing both shear-thinning and shear-thickening responses, which can be controlled by their catenation topologies. At larger strains, PAMs behave like lattices and foams, with a nonlinear stress-strain relation. At microscale, we demonstrate that PAMs can change their shapes in response to applied electrostatic charges. The distinctive properties of PAMs pave the path for developing stimuli-responsive materials, energy-absorbing systems, and morphing architectures.
H.B. Gemeda, N. A. Dudukovic, C. Zhu, A. Guell Izard, A. E. Gongora, J. R. Deotte, J. T. Davis, E. B. Duoss, E. J. Fong (2024), Hierarchical Composites Patterned via 3D Printed Cellular Fluidics, Advanced Materials Technologies
Additive manufacturing of freeform structures containing multiple materials with deterministic spatial arrangement and interactions remains a challenge for most 3D printing processes, due to complex fabrication tool requirements and limitations in printability of some material classes. Here, a versatile method is reported to produce architected composites using the concept of cellular fluidics, in which lattices of unit cells are used as templating scaffolds to guide flowable infill materials in a programmed spatial pattern, upon which they are cured in place to produce a deterministically ordered multimaterial solid. The lattice design relies on the unit cell size, type, strut diameter, surface wetting, and distribution of cellular structures to control liquid flow and retention. Individual unit cells are tuned to achieve reliable infilling and combined into higher-order architectures to achieve multiscale composite materials with disparate mechanical properties, including those considered non-printable. Lattice design considerations for leveraging capillary phenomena and demonstrate several methods of patterning polymers in 3D-printed cellular fluidic structures are presented. The concept of tuning the compressive response of an architected composite using a flexible-elastomer as the lattice and a stiff-epoxy as the infill material is illustrated.
CH. Lin, A. Guell Izard, L. Valdevit, Y. Won (2020), Mechanically Compliant Thermal Interfaces Using Biporous Copper‐Polydimethylsiloxane Interpenetrating Phase Composite, Advanced Materials Interfaces
Thermal interface materials are essential for thermal management in electronics packaging by providing a low resistance thermal pathway between heat sources and heat sinks. Nanostructured materials can be potential candidates for the next‐generation interface materials by coupling their high thermal conductivity and mechanical compliance, suppressing failure even after large numbers of thermal cycles. This work investigates the thermal and mechanical characteristics of a new type of thermal interface materials, consisting of metal/elastomer interpenetrating phase composites. The 3D, highly porous copper scaffolds are fabricated via a fast and simple in situ bubble‐templated electrodeposition process without the presence of solid templates; subsequently, the void fraction of the composite is filled by elastomer infiltration. The presence of elastomer matrix demonstrates limited impact on the thermal conductivity of the composite while it contributes substantially to the mechanical properties, providing the structural flexibility required. Thermal resistance values of 1.2–4.0 cm^2 K / W are measured upon multiple thermal cycles, confirming the mechanical stability of the composite, without showing any noticeable degradation.
J. Bauer, A. Guell Izard, Y. Zhang, T. Baldacchini, L. Valdevit (2020), Thermal Post-Curing as an Efficient Strategy to Eliminate Process Parameter Sensitivity in the Mechanical Properties of Two-Photon Polymerized Materials, Optics Express
Two-photon polymerization direct laser writing (TPP-DLW) is one of the most versatile technologies to additively manufacture complex parts with nanoscale resolution. However, the wide range of mechanical properties that results from the chosen combination of multiple process parameters imposes an obstacle to its widespread use. Here we introduce a thermal post-curing route as an effective and simple method to increase the mechanical properties of acrylate-based TPP-DLW-derived parts by 20-250% and to largely eliminate the characteristic coupling of processing parameters, material properties and part functionality. We identify the underlying mechanism of the property enhancement as a self-initiated thermal curing reaction, which robustly facilitates the high property reproducibility that is essential for any application of TPP-DLW.
C. Crook, J. Bauer, A. Guell Izard, C. Santos de Oliveira, J. Martins de Souza e Silva, J. B. Berger, L. Valdevit (2020), Plate-nanolattices at the Theoretical Limit of Stiffness and Strength, Nature Communications
Though beam-based lattices have dominated mechanical metamaterials for the past two decades, low structural efficiency limits their performance to fractions of the Hashin-Shtrikman and Suquet upper bounds, i.e. the theoretical stiffness and strength limits of any isotropic cellular topology, respectively. While plate-based designs are predicted to reach the upper bounds, experimental verification has remained elusive due to significant manufacturing challenges. Here, we present a new class of nanolattices, constructed from closed-cell plate-architectures. Carbon plate-nanolattices are fabricated via two-photon lithography and pyrolysis and shown to reach the Hashin-Shtrikman and Suquet upper bounds, via in situ mechanical compression, nano-computed tomography and micro-Raman spectroscopy. Demonstrating specific strengths surpassing those of bulk diamond and average performance improvements up to 639% over the best beam-nanolattices, this study provides detailed experimental evidence of plate architectures as a superior mechanical metamaterial topology.
J. Bauer, C. Crook, A. Guell Izard, Z. C. Eckel, N. Ruvalcaba, T. A. Schaedler, L. Valdevit (2019), Additive Manufacturing of Ductile, Ultrastrong, Polymer-Derived Nanoceramics, Matter
Ceramics would be ideal engineering materials if their brittleness and scattered fracture strength could be overcome. While ductility and extraordinary strength have been reported at the nanoscale, they both rapidly disappear when samples reach micrometer dimensions; furthermore, manufacturing is limited to elaborate approaches, which are purely scientific in nature. Here, we present a robust route to additively manufacture ductile, ultrastrong silicon oxycarbide (SiOC) via two-photon polymerization direct laser writing (TPP-DLW) of a preceramic resin and subsequent pyrolysis. We 3D-print micrometer-size pillars and architected materials with feature sizes down to ∼200 nm and characterize them under uniaxial compression. Independent of size, SiOC micropillars consistently deform plastically with strains up to 25% and strengths >7 GPa, across the entire range of examined diameters (1–20 μm). Our findings demonstrate straightforward fabrication of ductile, ultrastrong ceramics at previously unprecedented scales, potentially enabling manufacturing of engineering systems up to tens of millimeters in size.
J. Bauer, A. Guell Izard, Y. Zhang, T. Baldacchini, L. Valdevit (2019), Programmable Mechanical Properties of Two-Photon Polymerized Materials: From Nanowires to Bulk, Advanced Materials Technologies
Two‐photon polymerization direct laser writing (TPP‐DLW) is the most promising technology for additive manufacturing of geometrically complex parts with nanoscale features, and could dramatically accelerate the development of a wide range of engineering micro/nanosystems. However, a major obstacle to TPP‐DLW's widespread industrial adoption is the lack of systematic data on material properties and limited knowledge on their correlation with processing parameters. These correlations for the acrylate‐based resin IP‐Dip are experimentally established over a large range of process parameters and length scales ranging from nanometers to centimeters. Universal characteristic relations between mechanical properties and process parameters are identified, which enable the tailoring of the material strength and stiffness over half an order of magnitude from rubbery soft to hard and strong. With a threshold‐based optics model presented herein, the mechanical properties of the two‐photon polymerized material can be accurately captured as a function of the applied process parameters, laying the foundation for a universal quantitative predictability of two‐photon polymerization with programmable mechanical properties. This knowledge enables fabrication of microscale components with tailored local gradients in their mechanical properties, with significant implications for the development of novel mechanical, photonic, and photonic metamaterials.
L. Salari-Sharif, B. Haghpanah, A. Guell Izard, M. Tootkaboni, L. Valdevit (2019), Negative-Stiffness Inclusions as a Platform for Real-Time Tunable Phononic Metamaterials, Physical Review Applied
We propose an approach for real-time manipulation of low-frequency phononic band gaps in a metamaterial without affecting the material geometry, microarchitecture, or the crystal structure of the base material. Metamaterials with tunable band gaps are realized by introducing periodically arranged negative-stiffness inclusions, the modulus of which can be varied in time in order to modify the metamaterial macroscopic stiffness in certain directions without bringing the material to the point of elastic instability or inducing extreme geometric change. The evolution of band gaps is investigated numerically, and the proposed concept is verified experimentally in a lattice prototype with magnetic elements functioning as negative-stiffness units. Design guidelines for achieving a real-time tunable phononic band gap are also presented.
B. Haghpanah, A. Shirazi, L. Salari-Sharif, A. Guell Izard, L. Valdevit (2017), Elastic Architected Material with Extreme Damping Capacity, Extreme Mechanics Letters
We report on a new class of elastic architected materials with hybrid unit cells, consisting of discrete elastic elements with non-convex strain energy and one convex (but possibly nonlinear) elastic element, to obtain a reversible multifunctional material with extreme energy dissipation. The proposed design exploits numerically optimized nonlinearities in the force–displacement response of the sub-unit-cell elements to approach the theoretical limit of specific damping capacity in any material, ψth=8. Specific damping capacities up to ψ=6.02 were experimentally demonstrated, which are far greater than any experimental value previously reported, including in high damping elastomers (ψ<4.5). Remarkably, this damping performance is achieved even with a single unit cell, thus avoiding the need for thick multi-cell designs. Furthermore, the proposed design offers relatively high stiffness and low transmitted stress upon compression. The proposed concept could enable the design of reversible impact-resistant structures with superior crashworthiness and energy dissipation.